Revised Schedule‑M (2023–2025) doesn’t skim details. It now demands specific space allocations—e.g., 150 m² basic plus 100 m² ancillary for small volume injectables; 250 m² basic and 150 m² ancillary for large-volume parenterals using Form‑Fill‑Seal tech Laafon Galaxy Pharmaceuticals The Health Master+1. This is about more than regulatory compliance—it’s about competing internationally.
At a glance, this article dives into:
- Pros and cons of sticking with basic Schedule‑M vs. going above-and-beyond with WHO/FDA norms.
- Realistic cost tables.
- Step‑by‑step layout decisions.
- A mini case study for guidance.
- A comparison table, FAQs, and bold CTAs to turn readers into action-takers.
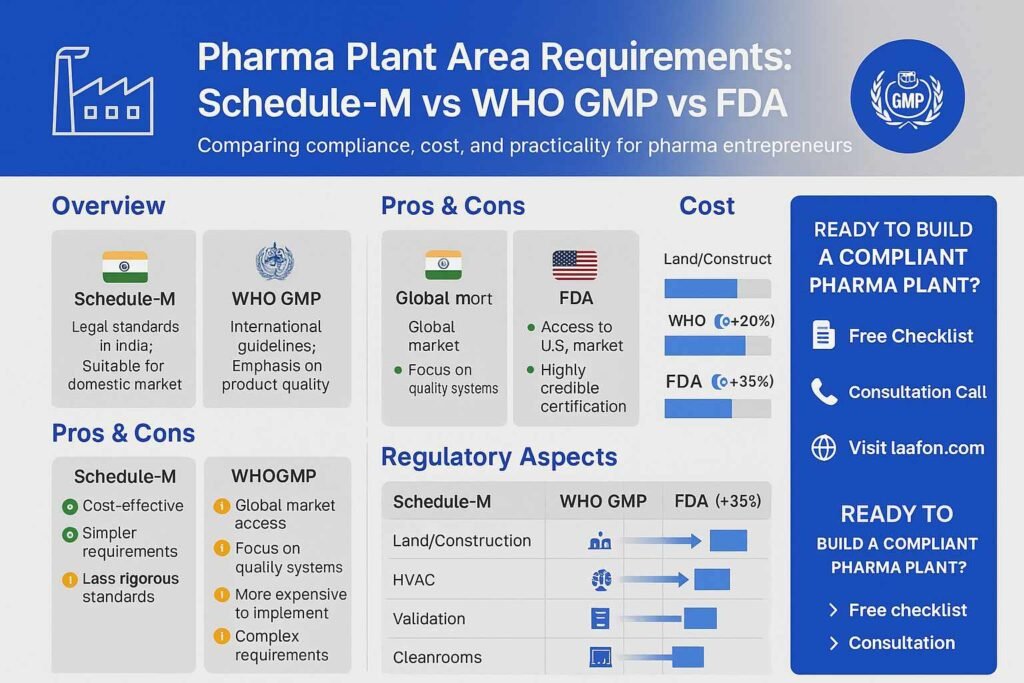
Option Breakdown: Pros & Cons
A. Baseline Schedule-M Compliance
Pros:
- Legally required, avoids government crackdowns.
- Cheaper land and build-outs vs. oversized international layouts.
- Speeds up approvals.
Cons:
- Risk of export rejection if layout doesn’t meet foreign buyers’ expectations.
- No room for future scaling or innovation.
- Keeps you in a reactive compliance mode—not proactive quality culture.
B. Schedule-M + WHO-GMP Alignment
Pros:
- Cleanroom sizing, environmental zones, storage conditions mirror international expectations [1]
- Facilitates smoother audits and global certification.
Cons:
- Higher initial capital cost for HVAC, controlled environments.
- Requires expert planning, risk mapping, validation—not nimble.
C. Schedule-M + ISO/cGMP (e.g., US FDA)
Pros:
- Opens doors for US market access; ensures manufacturing reliability[2]
- Builds a quality-first ethos that supports scaling.
Cons:
- Top‑tier investment in equipment, documentation, facility.
- Overkill if you’re focusing only on domestic or low‑cost generic markets.
Cost Breakdown
Let’s fast-track to hard numbers. Tables simplify comparisons (estimated, INR/sq ft):
Component | Schedule-M Only (₹/ft²) | WHO-GMP Enhancements (+20%) | cGMP Enhancements (+35%) |
---|---|---|---|
Land & civil work | ₹1,500 | ₹1,800 | ₹2,000 |
HVAC & environmental controls | ₹800 | ₹1,000 | ₹1,200 |
Cleanroom airlocks & segregation | ₹600 | ₹800 | ₹1,000 |
Validation/documentation | ₹200 | ₹300 | ₹400 |
Estimated total per ft² | ₹3,100 | ₹3,900 | ₹4,600 |
Total for a 10,000 ft² plant:
- Schedule‑M: ₹31 million ($370k)
- + WHO‑GMP: ₹39 million ($465k)
- + cGMP: ₹46 million ($550k)
Note: These are benchmark estimates; real numbers depend on geography, supplier quotes, and currency. But they show the step-up cost premium clearly—not overwhelming, but material.
Step-by-Step Decision Guide
- Clarify purpose: Domestic generics only? Export-focused? Biotech? Start with the end-use.
- Map product type: Tablets require 30 m²; capsules 25 m² + ancillary; parenterals need segregated areas, airlocks.
- Define capacity: Annual volume drives footprint—don’t just buy bare minimum.
- Regulatory gap analysis: Compare local floor plan vs. WHO/FDA to identify retrofitting field.
- Budget stress‑test: Factor 20‑35% buffer over construction for validation, deviations, documentation.
- Phased rollout plan:
- Phase 1: Humble Schedule‑M compliance.
- Phase 2: Add WHO-grade segregation & environmental controls.
- Phase 3: Full cGMP validation, digital QMS.
- Validation documentation: From Day 0, keep records—IQ/OQ/PQ, SOPs, logs.
- Mock audit: Run a self-assessment or hire consultant before regulatory inspection.
Case Study: “NovoGen Pharma’s Injectables Unit”
Background: NovoGen, a mid-tier Indian pharma making injectables (SVPs/LVPs), planned a new 5,000 ft² unit.
Phase 1 — Schedule-M baseline:
- Built a 150 m² basic zone + 100 m² ancillary for SVP production [3]
- Kept mixing, filling, packaging in dedicated rooms; cross-contamination logic applied as per Part I[4]
- Cost: ₹15M.
Phase 2 — WHO alignment:
- Added cleanroom-grade airlocks, humidity control per WHO GMP [5]
- Storage rooms retrofitted for controlled temperature and segregation [6]
- Additional ₹5M cost.
Phase 3 — Full cGMP-ready:
- Installed digital records, QMS, validation documentation.
- HVAC upgraded for differential pressures.
- Extra ₹4M for full readiness.
Outcome:
- Within 24 months, NovoGen cleared USFDA audit without major findings.
- Export contracts rose 40%, justifying upfront cost.
Comparison Table
(Already partially done in section 3; here’s a concise repeat with labels)
Option | Area Compliance | Investment | Export Readiness |
---|---|---|---|
Schedule‑M only | Minimum legal floor space | Low | Low |
+ WHO GMP | Added clean zones & storage | Medium (+20%) | Medium–High |
+ cGMP/FDA | Top-tier segregation & QMS | High (+35%) | Highest |
FAQ Section
It’s around 30 m² for basic installations; capsules require 25 m² + 10 m² ancillary
It’s around 30 m² for basic installations; capsules require 25 m² + 10 m² ancillary
How are parenteral area requirements defined?
SVPs need 150 m² basic + 100 m² ancillary; large-volume parenterals in plastic require even more (250 m² basic + 150 m² ancillary).
Does WHO mandate exact area sizes?
WHO GMP focuses on cleanroom classification, environmental control—not specific sizing (but implies segregation & space) [5].
What’s the key benefit of going cGMP?
Market access—for the US, EU—combined with comprehensive quality infrastructure[7].
Can existing plants retrofit vs. rebuild?
Yes—if layout allows phased upgrades, especially HVAC and segregation. But structural limitations may force rebuild.
Contact Us for Suggestions
Act now, or get left behind: Global buyers expect more than Schedule-M. Upgrade your plan—begin a gap analysis today.
References:-
- Schedule-M: Drug & Cosmetic Act-Page-442- Vijay Malik-Handbook-21st edition.
- Drug & Cosmetic Act-CDSCO official website.
- REGULATORY REQUIREMENTS FOR PHARMACEUTICAL PLANTS-bspublications.net